Continuous Improvement
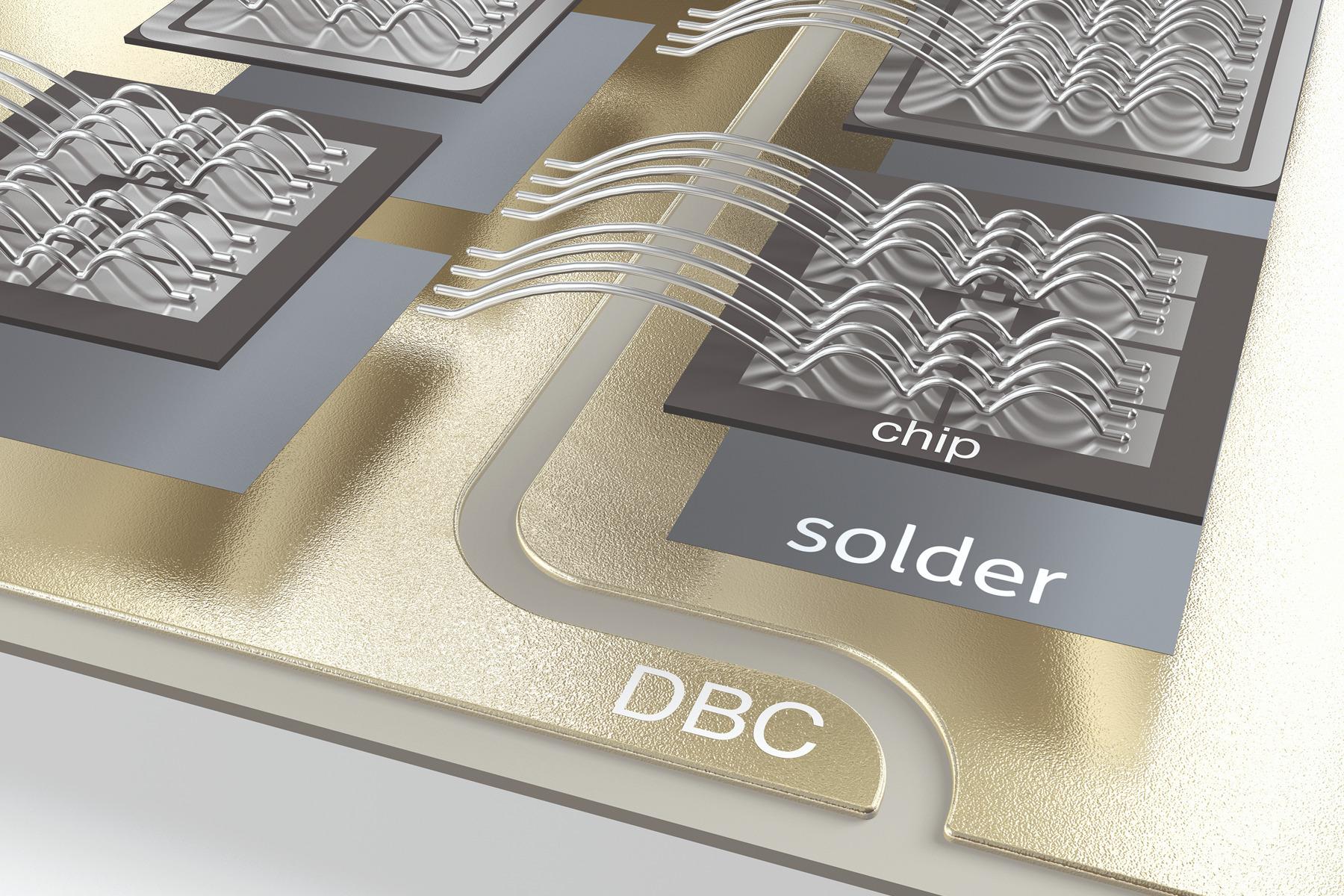
Solder has long provided a reliable bond between chip backside and substrate, as well as terminal and substrate. Solder is applied to the DBC substrate with a stencil, much in the same way PCB components are populated. Specialized ovens melt the solder to create the bond to the chip. Improvements in these ovens and production processes have resulted in modern modules exhibiting void-free solder connections in the millions of modules produced annually.
For chip frontside connection, aluminum bond wires are ultrasonically welded to a layer of aluminum on the chip surface. Ongoing research into power cycling wear-out mechanisms has led to optimization in both wire diameter and bond wire aspect ratio. These improvements continue to improve advance the reliability of standard connection technologies. Semikron Danfoss also makes use of aluminum-clad copper bond wires. These wires have the increased power cycling capability of copper while maintaining the cost-effective production process of aluminum bond wires.