Goodbye, Bond Wires
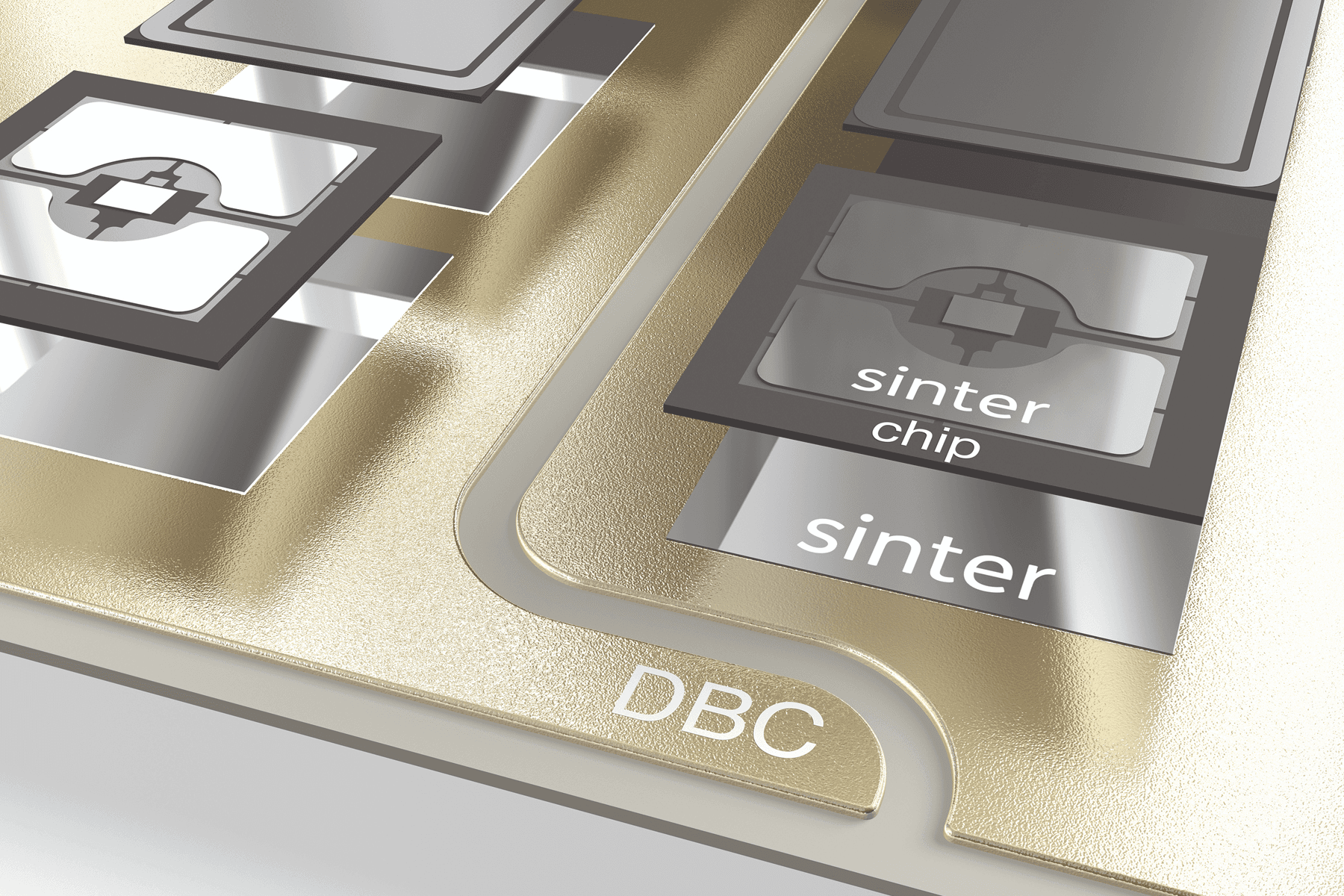
Double Sided Sintering Technology is a natural evolution of Single Sided Sintering Technology, which has already solved the weakness of the backside connection. The frontside connection of most industrial power semiconductor chips is achieved through ultrasonically welded aluminium wire bonds. With the backside connection replaced with silver sinter, these wire bonds are the new weak point. To remedy, Semikron Danfoss has combined their sintering technology with a flexible foil. This flex-layer replaces both the bond wires on the chip and between sections of the DBC substrate. The foil allows nearly the entire frontside surface of the chip to be used as an electrical connection. This provides a far more robust connection than the point contact of a wire bond, making it highly resilient to power cycling. The large surface area also improves the surge current handling of the circuit.
Aside from improving reliability, this technology is extremely beneficial for high-speed switching. The use of the wide, flat flex-layer as a conductor greatly reduces loop area in the commutation path. This dramatically reduces stray inductance and minimizes switching transients, making it an essential technology for packaging wide bandgap devices.